Paul Kwiatkowski is a passionate design and technology teacher at the International School of Nanshan Shenzhen. Constantly driven by a desire to learn and innovate, Kwiatkowski is always working on new projects and developing cutting-edge curricula. His teaching approach offers students extensive opportunities to explore, create, and hone their technical and creative skills. By integrating hands-on learning with real-world applications, he inspires students to think critically and push the boundaries of design and technology.
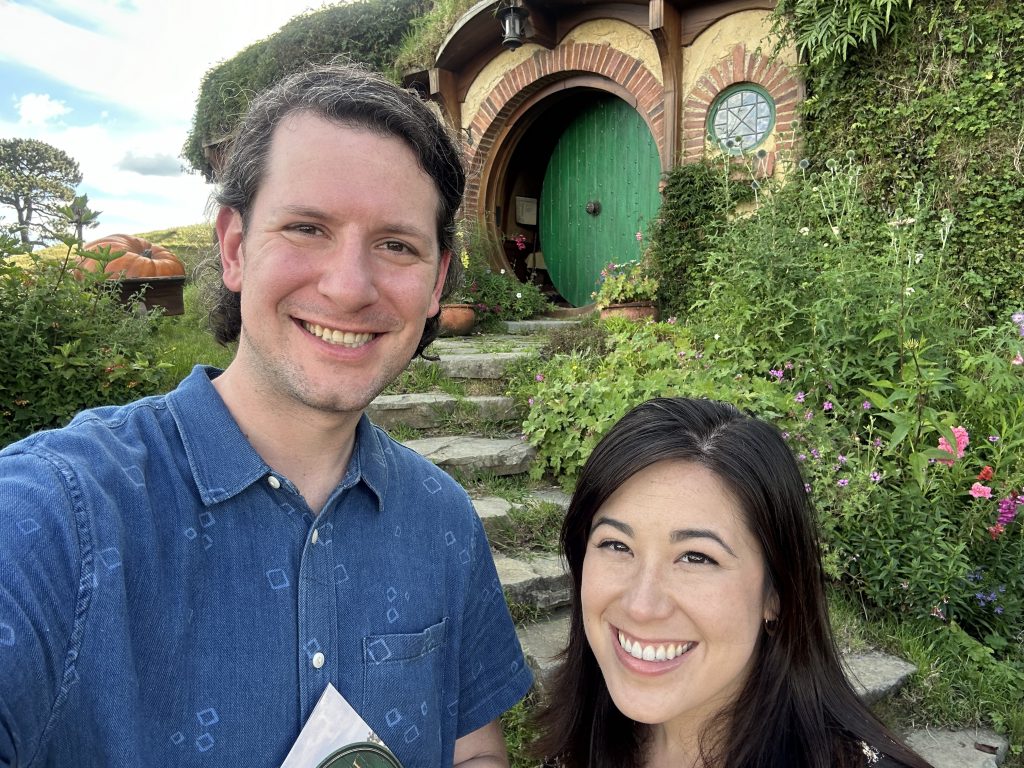
Project to be showcased: Halo Helmet
Paul Kwiatkowski’s Halo helmet project exemplifies his meticulous attention to detail and innovative approach. His projects range from highly detailed props like this helmet to practical 3D-printed solutions for his workshop. Alongside his personal endeavors, Kwiatkowski has developed an IB Design curriculum that inspires students to merge technical skills with artistic expression, producing a wide array of creative projects.
The Build Process
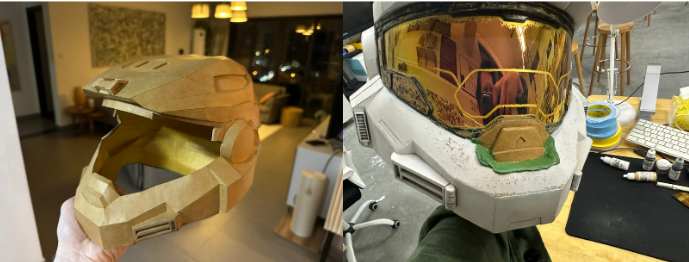
The journey began with the helmet’s seal and visor pattern, where early optimism about completion was soon met with the realization that more adjustments were necessary. A light coat of white paint revealed imperfections, particularly in the front ‘nose’ seal, which didn’t align with the rest of the helmet’s manufactured look. This led to a complete rebuild of the nose using card elements and green epoxy for a better fit.
Once the exterior was finalized, the helmet received its first official paint layers—a dark grey base followed by black and medium grey. After consulting with his wife, Kwiatkowski decided on an ‘Olive Recruit’ coloring, inspired by the design from Halo Infinite. This choice required several layers of green paint, with Vaseline used to create realistic wear and tear effects. Despite some challenges with paint opacity, the final tone was close to his vision, with weathering adding the final touches.
Finishing Touches
Applying AV Vallejo Matt Varnish proved to be a pivotal step, removing the glossiness from the paint and giving the helmet a worn, metallic look. This finish unified the helmet’s components and added a layer of protection, making it a believable prop.
The visor, a persistent challenge, required several attempts to achieve the desired look. After experimenting with gold paints and stencils cut by a laser cutter, Kwiatkowski had to make multiple touch-ups to maintain the visor’s integrity. The interior was finished with dark grey paint and liberal varnish, and padding was added using velcro, allowing for future modifications like a fan or microphone. A final detail was adding mesh to the front vents, enhancing the helmet’s depth and realism.
Lessons Learned
Through this project, Kwiatkowski learned the advantages of using epoxy putty over fibreglass for cleaner finishes, the value of laser cutting for precise detailing, and the critical role of matte varnish in achieving a realistic look. Timing and careful planning for visor details and accurate model references were also key takeaways, ensuring the helmet met his high standards.
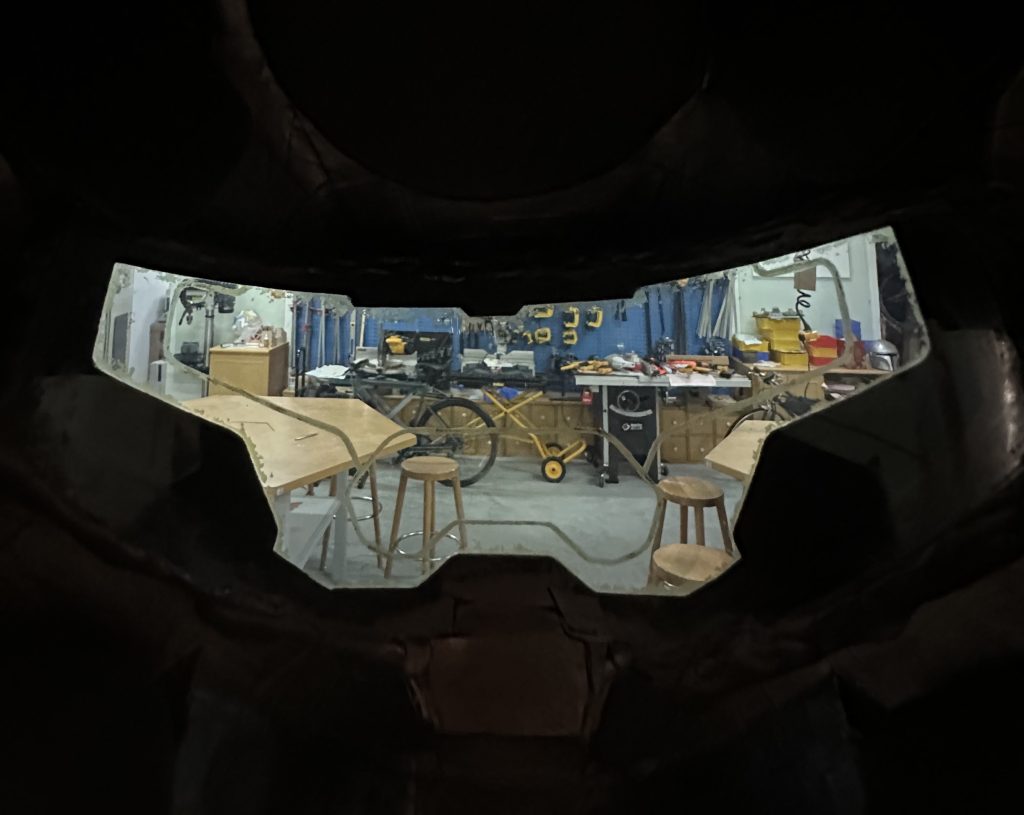
Click here for more details about the way Paul Kwiatkowski created the amazing Halo Helmet.